Case Study
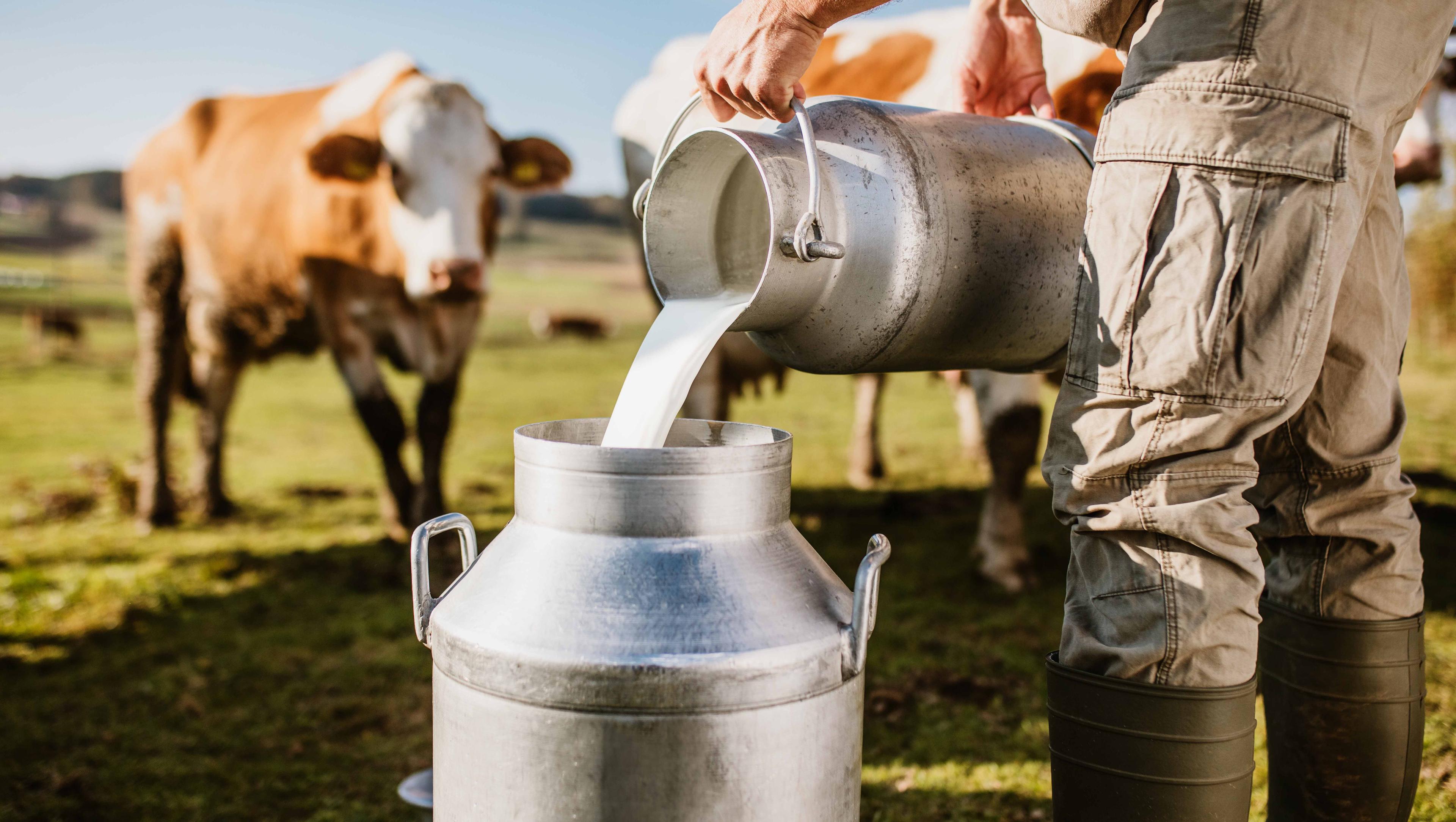
From Farm to Table: Data Utilization & Vendor Management for Maximum Efficiency
The leading Northern Nevada based dairy that provides local milk straight from local farmers and cows in Reno, NV. They are one of the oldest dairies in Northern Nevada with deep roots to the community, starting more than a century ago with just two milkers and a few cows. Now they produce a wide variety of products like milk, sour cream, cottage cheese, cream, and seasonal items like eggnog. They pride themselves on nourishing bodies and lives, and nourishing their communities.
The Challenge
The company is headquartered in Reno, NV and utilizes a milk jug manufacturer in Tracy, CA. Prior to working with ITS, requests for milk jug shipments were sent via email, and the manufacturer’s schedule didn’t always line up ideally with the dairy’s production schedule. There were also issues with shipments not being ready to be picked up on time, which led to running empty trailers and added costs. When containers weren’t available to put the milk in, the company would need to shut down production and perform a deep clean process to get up and running again at the cost of $10,000 per day.
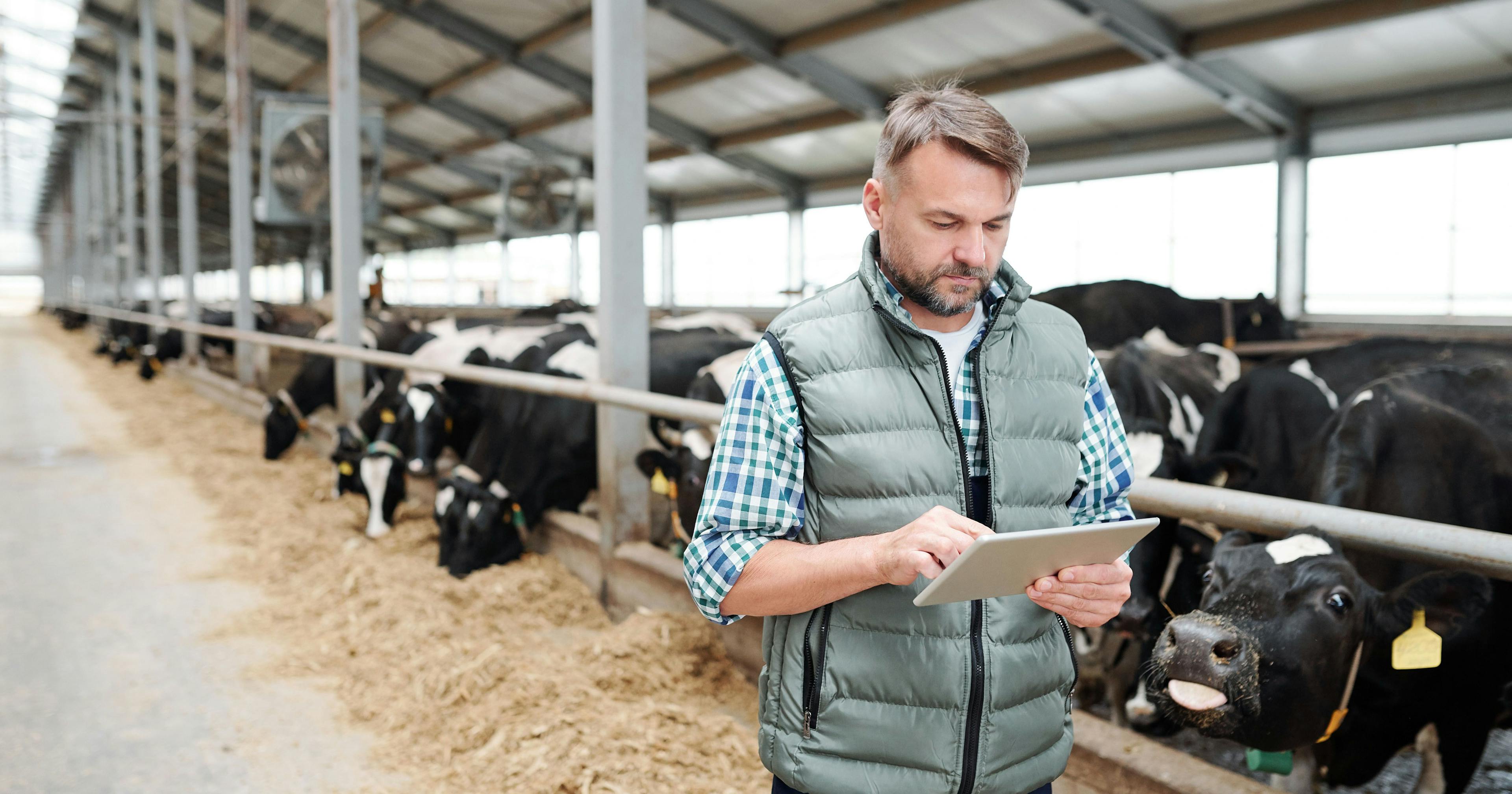
The Solution
ITS Logistics developed a centralized data system with shared access between all parties that includes all necessary details for each load, including the assigned driver, BOL, trailer numbers, and more. Additionally, ITS initiated weekly phone calls with the milk jug manufacturer and the dairy. This new process helped in several ways. It highlighted existing inefficiencies within the network, helped track exact trailer locations, and increased visibility and accountability to ensure maximum effectiveness from manufacturing to production. The team at the dairy now runs the weekly phone calls and uses shared data to keep track of all shipments and ensure milk jugs get to the production facility perfectly aligned with their production schedules. It also encourages timely communication in the event shipments get delayed due to extreme weather or traffic accidents on I-80.
This solution established a defined process where shipments are ready according to the production schedule, drivers arrive at the ideal times for pickups, trailers are accurately accounted for, and communication is improved with quick responses to disruptions in the supply chain. Executives at the dairy can now better understand the ins and outs of the logistics process and are able to increase communication and efficiency across the entire operation resulting in less disruptions to production.
The ability of ITS to really dig into our network and pain points and offer an improved solution has allowed us to streamline our communication, identify problems and bottlenecks within our supply chain, and ultimately, increase the efficiency of our overall operation. We truly value our partnership with them.
If you are looking for a creative logistics solution and a long-term transportation partnership, contact ITS Logistics today.