Sole Source Case Study
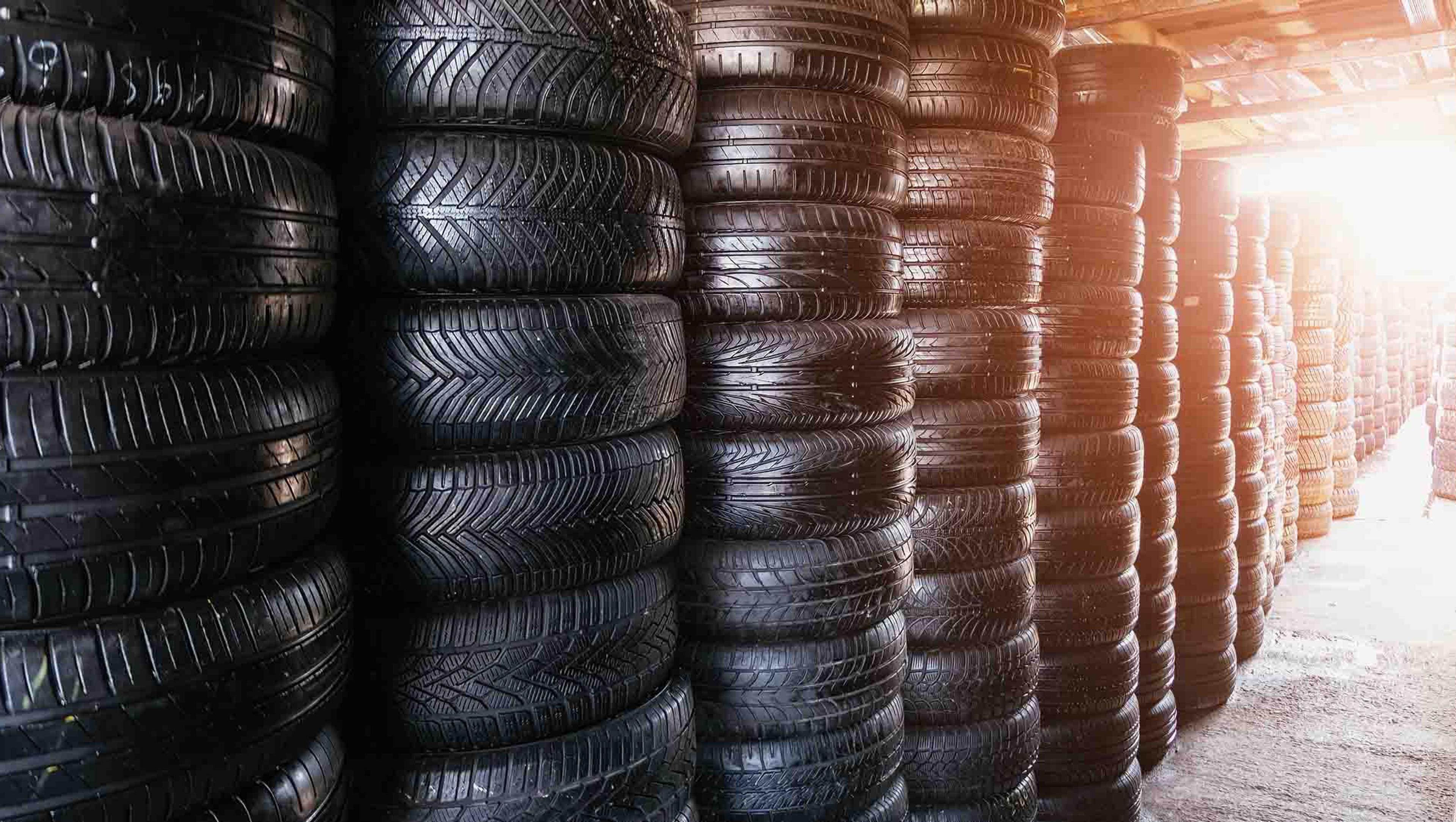
Sole Source Provider: Reducing Demurrage & Detention by Tens of Millions of Dollars
During the peak of historically high port congestion caused by the COVID-19 pandemic, a global, industry-leading tire company struggled to manage its annual import volume of approximately 30,000 containers. Packed ports and a lack of visibility hampered efficient container retrieval, resulting in tens of millions in demurrage fees.
Overflowing distribution centers and cluttered yards with a mix of full and empty containers further complicated the situation, leading to rapid per diem accumulation. Additionally, pre-existing ocean liner contracts restricted the company’s ability to take control of its drayage operations and manage the crisis effectively.
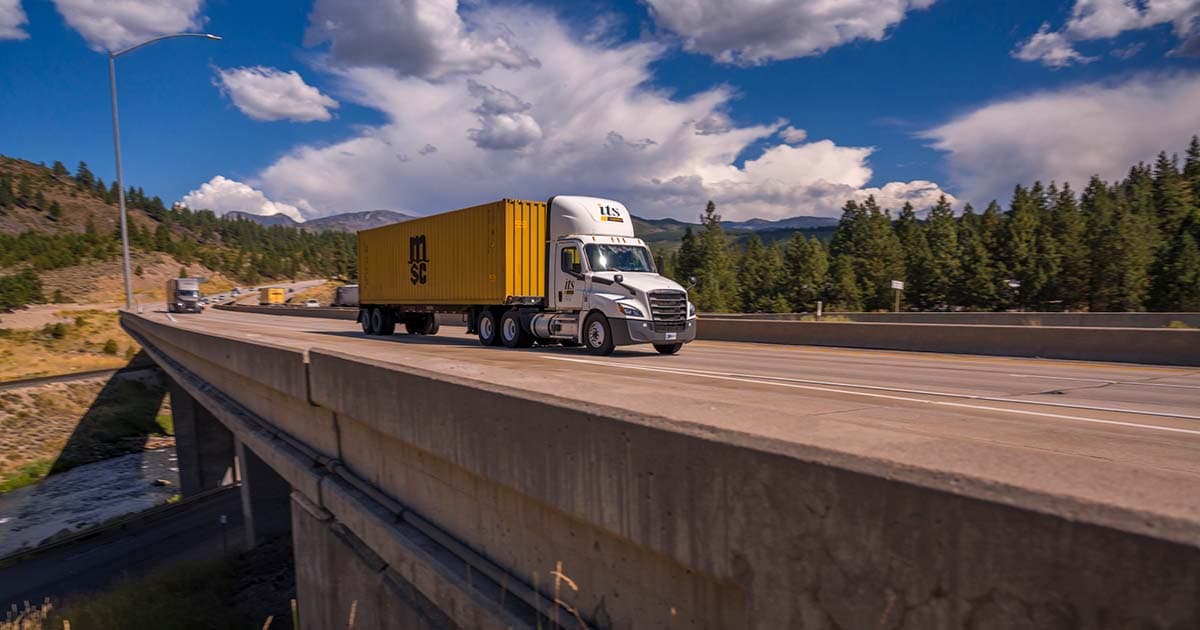
Solution
ITS proposed a plan for the customer to establish:
- One container drayage provider as a single point of contact.
- Long-term control of final-mile drayage with a reliable, sole-source provider without having to add supporting staff.
- A technology stack with end-to-end visibility and seamless integration.
- ITS as the company’s customer nominated trucker, allowing the team to work within existing contracts.
ITS prioritized stopping the accumulation of demurrage and detention fees and sent an onsite team to help reorganize the company’s most congested West Coast distribution center. The team worked to organize the overflowing yard, separating full and empty containers so that empties could be returned to port and terminated.
To work within existing ocean liner contracts, the tire company nominated ITS as its customer nominated trucker, giving the team the ability to dray containers out of the ports. Since ITS was already set up with every major NVO and ocean carrier, this was completed within 48 hours.
ITS established offsite pop-up yards and began a mass pulling of containers from the port to stop the accumulation of demurrage. The team also created a shuttle system from the pop-up yards to the reorganized distribution center to efficiently terminate empty containers from the DC, stopping per diem.
Another pop-up yard handled containers destined for the tire company’s inland DCs. This pop-up yard acted as a cross-dock facility, transferring products from containers to middle-mile carriers. This ultimately allowed the product to reach its intended inland DCs while maintaining the timely termination of containers.
Based on the success of the project with the first DC, the customer chose ITS as their sole-source drayage provider for every region and began integrating the ITS solution across their entire North American network.
Reporting and the Creation of a Platform
Throughout the project, ITS made routine reports to the customer to give them complete visibility into their operations. This process involved scrubbing large amounts of data and inspired the ITS team to innovate a tech solution, which led to the development of ContainerAI.
ITS developed ContainerAI as a container management and visibility platform built from an operator’s mindset, combining 25 years of operational experience with machine learning, best-in-class data, and customer-focused reporting.
The launch of ContainerAI provided the customer and the ITS team with visibility into ocean voyages, rail transport, and trucking milestones. It also gave the customer a way to prioritize containers that were the most at risk of accruing detention and demurrage, which reduced future fees and created greater operational efficiency.
After the success of the platform, ITS would later roll out ContainerAI to all drayage customers and provide it at no additional charge for all loads managed by ITS Logistics.
Results
Through the support of the company’s partnership with ITS, the company was able to save tens of millions of dollars in demurrage and detention fees and re-establish import flow to its North American supply chain.
Due to the success of the partnership, ITS Logistics became the sole drayage provider for the company, establishing a single point of contact and streamlining processes for the company’s port and rail ramp operations.
In the following year of the partnership, the company experienced additional savings as ITS’s approach created even more efficiencies and drove down transportation costs by 50%.
- Reduced demurrage and detention fees by millions of dollars per week.
- Re-organization of DCs and enhanced efficiency.
- Improved network visibility provided through ContainerAI.
- Greater operational efficiency through a sole-source provider.
- Reduced administration burden without having to add staff.
- Savings the following year from ITS driving down transportation costs 50%.