How to Leverage Technology in Logistics and Supply Chain
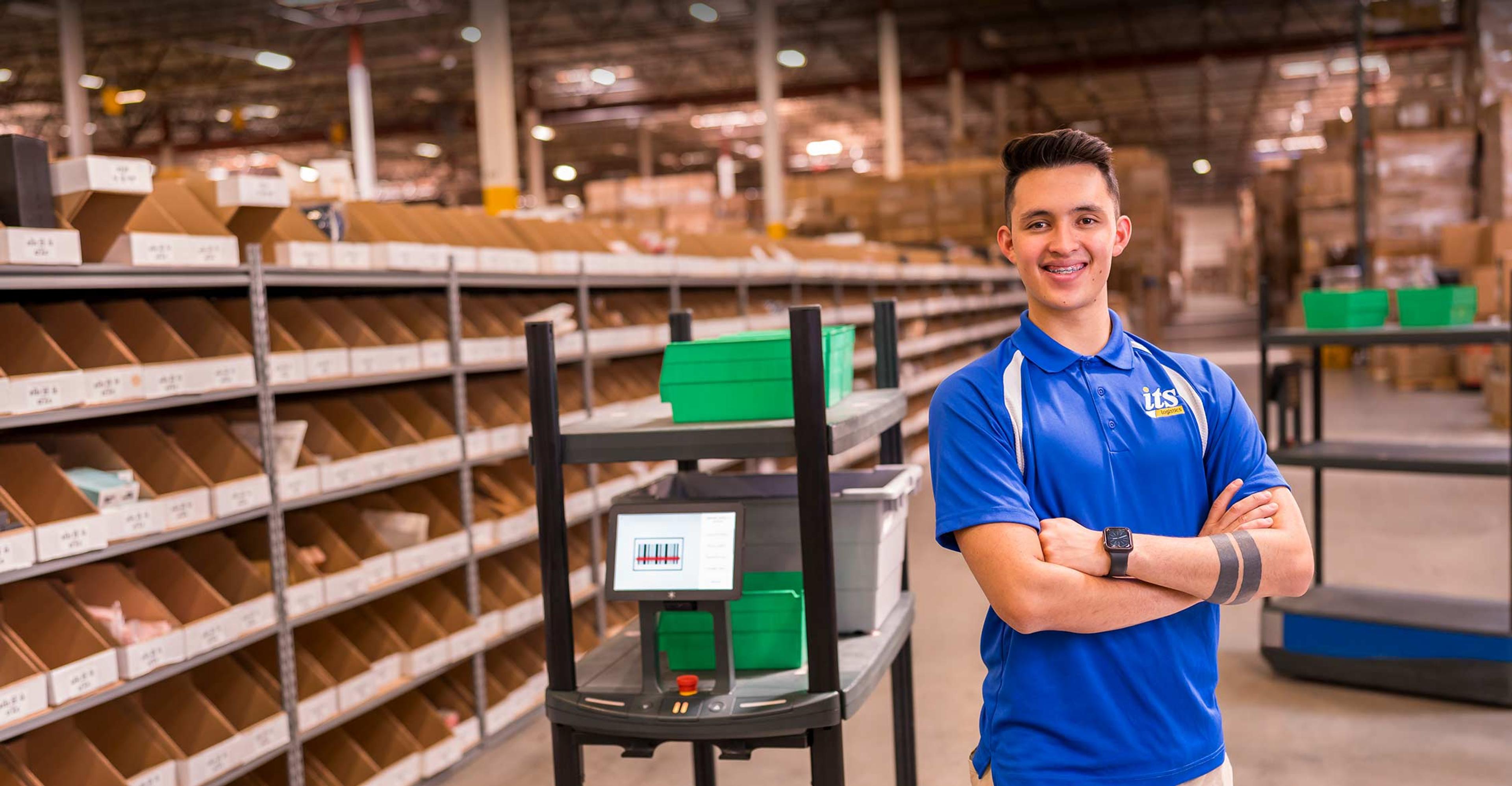
It’s no secret that technology in logistics and supply chain can be a key differentiator in the industry. Access to real-time data for freight visibility, order status updates and the enhanced ability to make data-driven decisions are extremely important for a successful business— effective technology can help with all of this. According to the 2023 Annual Third-Party Logistics Study, 75 percent of shippers state technology plays a greater role in evaluations and selection of 3PLs.
How can technology help with my logistics operations?
The right supply chain technology can be life-changing for business operations. It can help with everything, from streamlining and optimizing warehouse management and fulfillment methods to visualizing order data on real-time dashboards. If a high volume of orders require pick and pack fulfillment, technology like robot-led sortation, put-to-light systems and high-speed sortation systems that are capable of thousands of item sorts per minute can increase efficiency by large percentages. The right technology stack can be instrumental in optimizing the picking workflow. This can help fit the most product into the least amount of space and maximize efficiency through the entire order fulfillment process. It can also allow performance metrics to be shared such as order processing times, order status and lot tracking with shareholders, improving visibility and allowing data to drive decision-making processes.
3PLs have been increasing technology solutions and enhancing technology capabilities to keep up with shipper demands and a list of “must haves.” Shippers have simultaneously become more proficient buyers of technology solutions, and the bar is continuously being raised. Both shippers and 3PLs should be focusing on how to best leverage the technology readily available, especially as the industry is still resetting from the disruptions of 2020-2022. Supply chains need to reset, rebalance, and embrace the back-to-basics.
Technology will help you stay competitive
No matter what kind of fulfillment services, from ecommerce to omnichannel to retail, consumer expectations are growing increasingly difficult to meet. According to Deloitte’s 2023 Retail Industry Outlook, six in ten executives foresee strengthening digital commerce offerings as a top growth opportunity.
Companies are consistently finding creative ways to stay competitive and meet customers’ shopping behaviors. Retailers should invest in technologies that provide a seamless purchasing experience within different channels and shoppable media to guide users to purchase and build loyalty. For example, 60% of Gen Z and 56% of millennials planned to use social media as part of their holiday shopping in 2022.
Therefore, it’s important to stay continuously innovative to sustain a competitive advantage. Adopting new technologies and methodologies to increase effectiveness across the board is the way to stay ahead of the competition.
Optimization starts with the right technology
The growing number of retailers and increasing customer expectations all mean that it’s vital that distribution processes are as efficient as possible. To have a truly integrated supply chain network is everything—from when a customer places an order to the pick and pack fulfillment process to shipping and delivery right down to the returns process, all accessible through real-time visibility. Evaluating each separate workflow will lead to the understanding of how to optimize a supply chain and increase overall efficiency. Ultimately, supply chain capabilities must be elevated to to serve the needs of customers while increasing efficiencies, reducing costs, and always improving the customer experience through technology.
The right technology can help ensure real-time flexibility
Maintaining a balance between a reliable and flexible supply chain is undeniably an important factor in success, but it can be extremely complex. When interruptions impact the industry, the capabilities to adjust and pivot for demand are vital. For example–ITS utilizes custom technology that balances single-unit orders and multi-unit orders as demand fluctuates. Real-time flexibility in situations like this is only possible by adopting effective technology—in fact, customers, vendors, and other supply chain partners expect it.
What technology to look for when outsourcing your fulfillment
When considering outsourcing fulfillment to a third-party logistics company, it’s extremely important to review the technology and logistics capabilities. Outsourcing to a 3PL is a great way to implement technologies without having to go through complicated onboarding in-house. Technology solutions can also be very expensive to research and implement in-house, and the process can be long and difficult. Using a 3PL’s expertise and existing technology stack can save valuable time and money. When vetting 3PLs, look at current capabilities, but also seek out partners who have customized technology solutions that can provide seamless, real-time order processing, end-to-end supply chain visibility and order status tracking. Additionally, look for solutions that increase operational efficiency at every level of the fulfillment process and offer real-time data visibility that will lead to more informed decisions. Not only should a provider have the technology solutions needed today—but make sure they are investing in what is coming next. For example, while EDI might be a current supply chain integration method, that is changing. Newer integrations like API offer live and real-time integrations. It’s very important to make sure a provider can keep up with ever-changing and updating technology solutions to ensure they can support scalable business needs.
How ITS Logistics can help you use technology as a competitive differentiator
ITS Logistics continues to invest heavily in logistics technology solutions for customers. The in-house development teams have the expertise to integrate with any shopping cart or order management system, allowing real-time inventory management, order status and shipping updates. The team can create custom software that helps increase efficiency in the order fulfillment process. A great example of this is Flexpick 2.0, created by in-house developers and consisting of proprietary picking and packing modules on an Azure Cloud server. These modules include batch singles, batch multi with put-to-light or put wall and traditional cluster cart picking. The software helps increase productivity and streamline client onboarding while creating the best and most cost-effective solutions. Because development is handled in-house, ITS creates custom updates and solutions that will best serve customers. The ITS robust business intelligence team also creates dashboards for customers that allow stakeholders to make immediate, data-driven decisions.
Interested in learning more about technology capabilities? Contact Kasia Wenker, ITS Logistics Director of Supply Chain Solutions today.