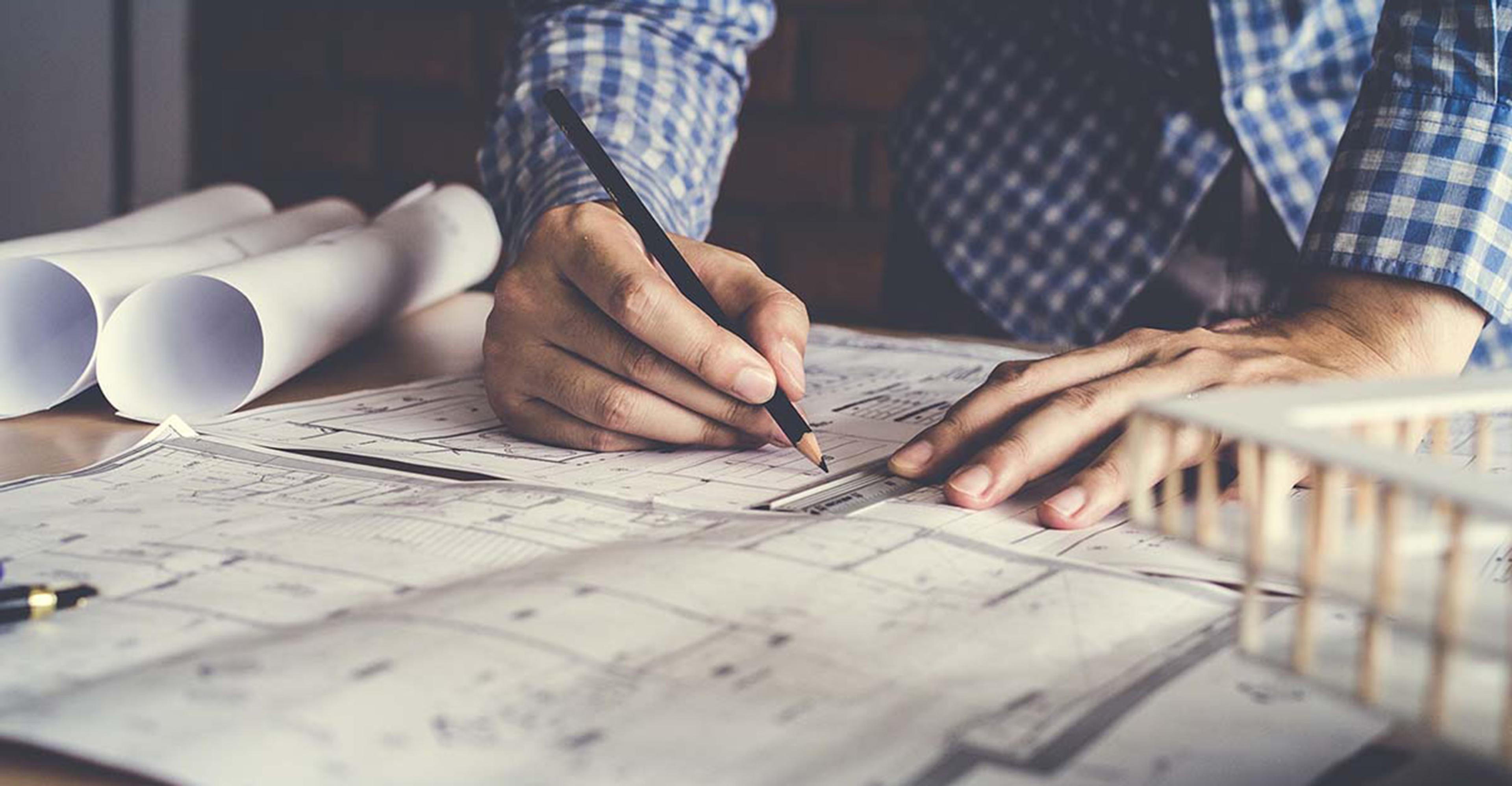
The Cost to Build a Warehouse
A primary consideration for most companies that manage product distribution and fulfillment is whether or not to build a warehouse. The cost of building a warehouse can seem straightforward, accounting solely for the cost of the actual building materials and professionals. Building a warehouse, however, comes along with a string of hidden soft costs in the long-term that may not be top-of-mind during the construction process. When determining whether to build a new warehouse or partner with a distribution and fulfillment provider, considering these hidden costs upfront can both simplify the decision process and decrease long-term operational costs.
What does it cost to build a warehouse?
When building a warehouse, a number of factors will influence construction cost—material choice, square foot needs, and storage needs are just a few of those factors. However, even with the hard cost accounted for, the cost to build a warehouse doesn’t stop there.
Once the new warehouse project is fully constructed and operational, there are additional, long-term costs to consider. Some are more traditional—utilities, maintenance, property management—while others are more unique. Effectively running the new warehouse building comes with variable staffing needs, technology resources, organization, and more.
The hidden soft costs of warehouse management
Whether building the company’s first industrial warehouse or its tenth, it can be easy to forget the associated long-term cost of opening a new distribution and fulfillment center. The excitement of bringing products closer to the customers creating demand can overtake the planning efforts. When looking at the soft cost of building a new warehouse, the following factors should be considered to support long-term ROI.
- Labor, training, and continuous education
As customer demand flexes throughout the year, so does warehouse staffing needs. The ability to scale the number of human resources working in distribution and fulfillment is vital. As more orders come in near peak season, temporary hires need to be made in order to maintain pacing. This flex in employment needs can be a challenge when warehousing is kept in-house, from both a labor availability and labor costs standpoint.
Beyond this, the demands of training and continuously educating a warehouse team can be high. Keeping the team producing efficiently requires refined processes that support overall supply chain efficiency. This effort requires a great deal of time and can significantly reduce the ROI of owning a warehouse. - Technology upgrades and support
A new warehouse will need a new technology stack. If the organization has a technology stack from years of warehouse management, this may not be a significant issue. However, for companies that are newer to warehouse management, or even well-practiced companies auditing current processes and programs, technology is an important factor to consider.
Insourcing your warehousing demands budget, time, and resources for an appropriate Warehouse Management System (WMS). The software chosen will need to effectively control the movement and storage of products in the warehouse, controlling the movement and storage of products and streamlining the distribution and fulfillment processes. Maintaining a WMS for the life of the building, as well as implementation and maintenance of any warehouse automation, should be budgeted for as long-term, necessary soft costs. - Organization/Industrial Engineering
The travel time inside of a warehouse can have a significant impact on ROI. Optimizing product location can improve storage and picking efficiency, but requires a significant time and resource commitment. At times, the process can require periods of trial and error and moving product and equipment. Ideally, the building will be organized following a strategy that reduces picker travel and creates more stable loads. - Security
The loss or theft of warehouse inventory can be a significant problem. In fact, according to CargoNet’s 2022 report, approximately $223 million in cargo was stolen across all cargo theft events in 2022. Of these events, warehouse theft accounts for the highest-value incidents due to the high level of product volume in one location.
Protecting against cargo theft in a new warehouse requires on-site security systems and, at times, personnel. These systems and human resources can be costly in both the short- and long-term.
There are other significant hidden costs in building a warehouse. Inventory shrinkage and damage, inaccurate shipments, reverse logistics, and dissatisfied customers all need to be considered in warehouse construction cost.
Maximizing ROI on Warehouse Space
As the cost to build a warehouse adds up, there are other options to consider. Partnering with a third-party logistics company can alleviate the hidden opearting expenses, providing a higher ROI and a fully managed distribution center.
A 3PL providing distribution and fulfillment services will already have the necessities in place. With access to temporary staffing for peak seasons, the concern around flexing labor and labor costs is removed. Additional human resources will be added as necessary, and properly trained, to ensure customer orders are filled on time.
Similarly, an established 3PL will already have a WMS implemented, relieving the company of the need to seek out new technology. Additionally, the 3PL will have a set of integrations available to send information back to the organization—including accurate inventory counts and other actionable data.
The right provider will also come with a customized plan for the company’s distribution and fulfillment, including proper organizational plans for maximized efficiency. They’ll be able to create dedicated space and flex to meet inventory needs.
Outsourcing to a 3PL Provider
ITS Logistics is a premier third-party logistics company, strategically located to provide distribution and fulfillment services to 95% of the US population in just two days. Each warehouse is AIB Certified, technologically enabled with best-in-class systems, and staffed to meet every fulfillment need.
What sets ITS Logistics apart is a hyper focus on customer service—providing fully customized solutions for each and every customer. Working to truly understand the different requirements of each company, ITS puts forward an in-depth and solution-oriented plan for distribution and fulfillment at the very beginning of the partnership.
If the long-term, operating expenses of managing a warehouse don’t make sense for the organization, ITS Logistics is the solution. Contact us today to speak with one of our experts and being crafting a customized distribution and fulfillment plan together.